¿Qué es el Sistema de Producción de Toyota y por qué es tan difícil de replicar?
El Sistema de Producción de Toyota (TPS) es considerado el estándar de oro en la manufactura, pero ¿por qué tantas empresas fallan al intentar replicarlo? En este blog, exploramos los principios clave de TPS, como Justo a Tiempo y Jidoka, y descubrimos por qué la cultura organizacional y el compromiso a largo plazo son cruciales para su éxito. Si estás buscando implementar el TPS en tu empresa, este artículo te ofrece estrategias prácticas para superar los desafíos. Continuar leyendo…
MEJORA CONTINUA
Daniel Cruz
8/19/20245 min read
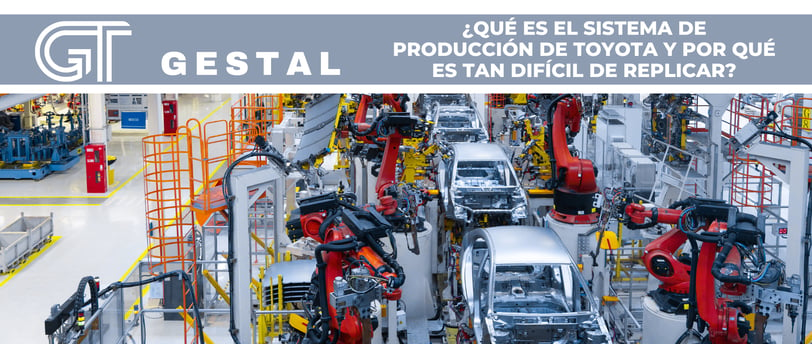
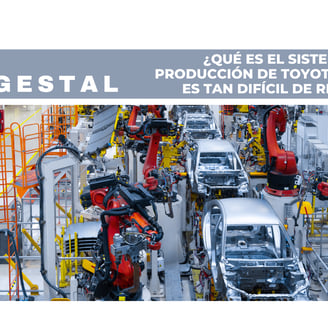
Cuando hablamos de eficiencia y excelencia en la manufactura, el nombre Toyota es casi sinónimo de perfección. El Sistema de Producción de Toyota (TPS) es ampliamente considerado como el estándar de oro en la industria manufacturera, y no es difícil entender por qué. Desde su desarrollo, el TPS ha permitido a Toyota convertirse en un líder mundial en calidad y eficiencia, estableciendo un modelo que muchas empresas han intentado replicar, con resultados a menudo menos exitosos.
¿Qué es el Sistema de Producción de Toyota?
El Sistema de Producción de Toyota es un enfoque integral para la manufactura que se basa en dos principios fundamentales: Justo a Tiempo (Just-In-Time) y Jidoka (automatización con un toque humano). Estos principios se combinan para crear un sistema que minimiza el desperdicio, maximiza la eficiencia, y asegura la calidad en cada etapa del proceso de producción.
Justo a Tiempo: Este principio se centra en producir solo lo que es necesario, cuando es necesario, y en la cantidad necesaria. Esto reduce el exceso de inventario y el desperdicio, manteniendo los costos bajos y la producción ágil.
Jidoka: Este concepto se refiere a la automatización inteligente que detiene el proceso de producción en caso de problemas, permitiendo que los errores sean corregidos inmediatamente. Esto asegura que la calidad esté integrada en el proceso de manufactura, en lugar de ser inspeccionada solo al final.
El TPS también se apoya en otras prácticas clave, como el Kaizen (mejora continua), que promueve la participación de todos los empleados en la mejora de los procesos, y el Kanban, un sistema visual para gestionar el trabajo en progreso y asegurar un flujo continuo en la producción.
Orígenes del TPS
El TPS fue desarrollado después de la Segunda Guerra Mundial por los ingenieros de Toyota, liderados por Taiichi Ohno, quien es ampliamente reconocido como el padre del sistema. En ese momento, Toyota enfrentaba limitaciones severas en recursos y necesitaba encontrar una forma más eficiente de producir automóviles que las líneas de producción en masa utilizadas por fabricantes occidentales como Ford.
Inspirados por las prácticas de inventario mínimo observadas en los supermercados de Estados Unidos, Ohno y su equipo diseñaron el TPS para eliminar el desperdicio, mejorar la calidad y responder rápidamente a la demanda del cliente. Este enfoque transformó a Toyota de un pequeño fabricante japonés en un gigante mundial, y el TPS se convirtió en un modelo a seguir para las industrias de todo el mundo.
¿Por qué es tan difícil de replicar?
A pesar de la apertura de Toyota en compartir sus prácticas, muchas empresas han fallado al intentar replicar el TPS con el mismo éxito. Aquí te explicamos por qué:
Cultura Organizacional: El TPS no es solo un conjunto de herramientas o técnicas, sino una cultura profundamente arraigada en Toyota. Las empresas que intentan copiar el TPS a menudo subestiman la importancia de la cultura de mejora continua y respeto por las personas que es central para su éxito.
Rigidez y Flexibilidad: Aunque el TPS establece reglas rígidas para la ejecución del trabajo y la relación entre trabajadores y proveedores, también fomenta una flexibilidad increíble para adaptarse a los cambios y mejorar constantemente. Muchas empresas no logran equilibrar esta paradoja, enfocándose demasiado en la rigidez o en la flexibilidad, pero no en ambas.
Compromiso a Largo Plazo: Implementar el TPS requiere un compromiso a largo plazo. Muchas organizaciones buscan resultados rápidos y abandonan el proceso cuando no ven mejoras inmediatas. Sin embargo, el TPS está diseñado para generar beneficios sostenibles a lo largo del tiempo, lo que requiere paciencia y perseverancia.
Método Científico: El TPS se basa en el método científico, donde cada mejora o cambio se trata como un experimento que debe ser probado y validado. Esta atención meticulosa al detalle y al aprendizaje constante es difícil de mantener, especialmente en empresas donde la cultura de la experimentación no está bien establecida.
Sugerencias para Implementar el TPS en tu Empresa
Aunque replicar el éxito de Toyota es un desafío, no es imposible. Aquí te ofrezco algunas sugerencias para superar las dificultades y lograr implementar el TPS en tu organización:
Adopta una Cultura de Mejora Continua: Fomenta una cultura donde todos los empleados, desde la alta dirección hasta el personal de línea, estén comprometidos con la mejora continua (Kaizen). Esto implica no solo la implementación de herramientas, sino también un cambio de mentalidad que valora la innovación, la eficiencia y el respeto mutuo.
Equilibra la Rigidez con la Flexibilidad: Es crucial mantener un equilibrio entre la estructura rígida necesaria para garantizar la consistencia y la flexibilidad para adaptarse y mejorar. Define procesos claros, pero también permite y fomenta que los empleados identifiquen y propongan mejoras.
Comprométete a Largo Plazo: La implementación del TPS no es un proyecto de corto plazo. Establece expectativas realistas y prepara a tu equipo para un viaje continuo de mejora. Asegúrate de que la dirección esté comprometida y que haya una visión clara de cómo el TPS beneficiará a la organización en el largo plazo.
Aplica el Método Científico: En lugar de ver las mejoras como simples cambios, trátalas como experimentos. Establece hipótesis claras, prueba los cambios, mide los resultados, y ajusta según sea necesario. Esta metodología garantiza que las mejoras se basen en datos y no en suposiciones.
Forma Equipos Multifuncionales: Crear equipos que incluyan personal de diferentes departamentos puede ayudar a romper los silos y garantizar que todas las partes del proceso de producción estén alineadas. Estos equipos pueden trabajar juntos para identificar cuellos de botella y proponer soluciones integrales.
Capacitación Continua: Invierte en la capacitación continua de tus empleados. El TPS requiere que los trabajadores tengan una comprensión profunda no solo de su rol específico, sino de cómo encajan en el proceso más amplio. Esto incluye habilidades técnicas y conocimientos sobre las metodologías del TPS.
Aprende de los Errores: No te desanimes por los fallos iniciales. Toyota no construyó su sistema de producción perfecto de la noche a la mañana. Usa cada error como una oportunidad para aprender y mejorar.
Conclusión
El Sistema de Producción de Toyota es más que una colección de herramientas y prácticas; es una filosofía de producción que ha demostrado ser increíblemente eficaz cuando se implementa correctamente. Aunque replicar el éxito de Toyota es un desafío, no es imposible. Con una cultura de mejora continua, un compromiso a largo plazo, y la aplicación disciplinada del método científico, las empresas pueden adoptar y adaptar el TPS para lograr una mayor eficiencia, calidad y competitividad en el mercado.
Implementar el TPS es un viaje, no un destino. Si tu organización está dispuesta a embarcarse en este camino, los beneficios pueden ser extraordinarios y sostenibles.